Product AI外観検査 SwitchOn
- ホーム >
- SwitchOn
少ない学習データで迅速なAI外観検査導入を実現
AIを活用した画像検査では、通常、多くの学習データが必要です。大量の学習用データの準備に手間がかかることが、AIによる外観検査の導入を阻害する要因となり大きな課題になっていました。しかし、SwitchOnの「DeepInspect」を利用すれば、少ない学習データで効率的に検査システムを構築することが可能です。 DeepInspectは、200枚以下のデータで学習を開始できるため、初期費用や工数を抑えつつ、スムーズに導入を進めることができます。これにより、導入時の初期検証の負担を大幅に軽減することが可能です。
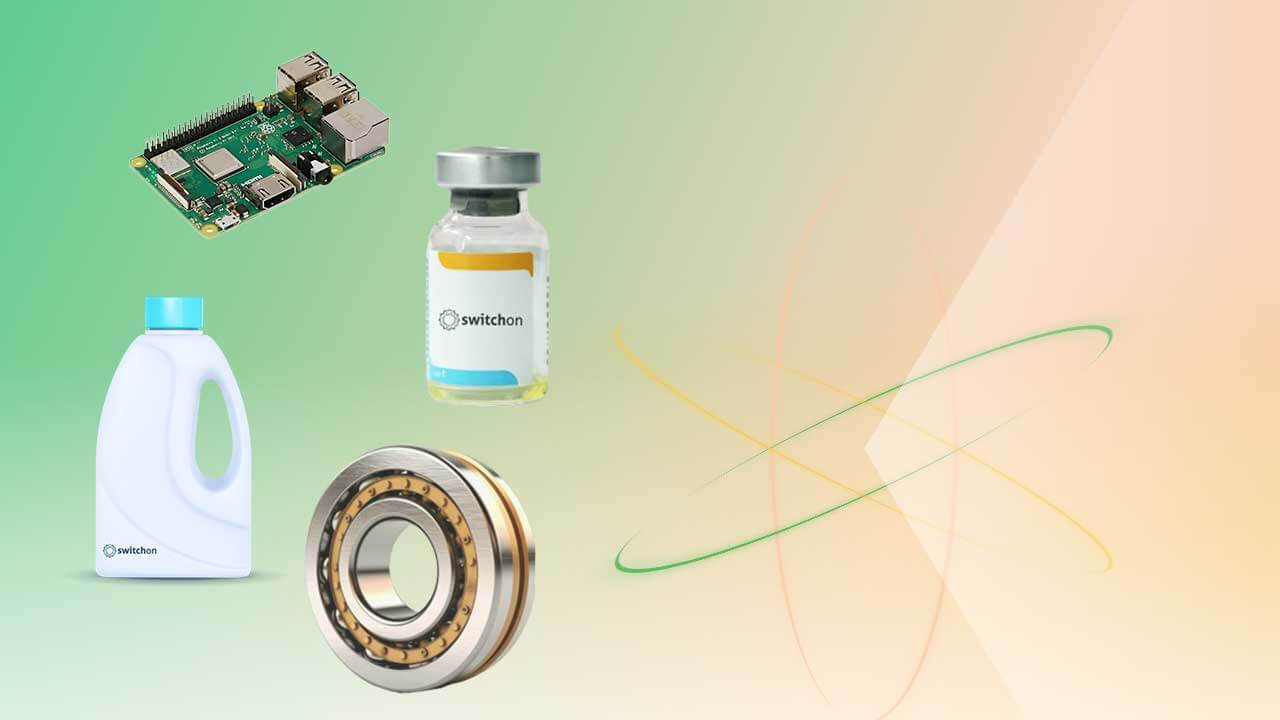
DeepInspectで行う学習、検査、分析までのプロセス
STEP1:学習
- AIモデル生成には200枚未満の良品画像から学習する事が可能です。少量のデータで効率的に学習を行うことができるため、初期準備における時間とコストの負担を大幅に軽減できます。
- ディープラーニングを活用した最新のアルゴリズムを採用しており、従来の手法よりも高精度かつ信頼性の高い学習が可能です。これにより、外観検査における品質管理において安定した性能を提供します。
- 新しいAIモデルのトレーニングは、およそ1時間で完了します。短時間でモデルを構築できるため、迅速な導入や改善サイクルを実現し、生産ラインの効率化に貢献します。
STEP2:検査
- 150ミクロンまでの微細な欠陥を99.95%以上という非常に高い精度で検出することが可能であり、さらに誤検出率は0.05%未満に抑えられています。この高精度な欠陥検出能力により、製造工程の品質を大幅に向上させることができます。
- 1分間に1000個以上の部品を高速で合否判定することができるAI検査システムを搭載しています。この高速処理により、大量生産ラインでも効率的かつ正確な検査が可能です。
- インライン検査はもちろんのこと、オフラインでの検査にも柔軟に対応可能です。これにより、さまざまな生産環境やニーズに合わせた運用ができ、幅広い用途に活用できます。
STEP3:分析
- 生産プロセスや製品品質に関する膨大なデータを深く掘り下げて解析することが可能です。この詳細な解析により、現場で見逃されがちな問題点や改善点を正確に把握することができます。
- 分析結果をまとめたレポートには、具体的なデータや傾向が詳細に記載されており、それらの情報をもとに現場の改善活動に直結する施策を立案・実行できます。これにより、品質向上や生産性向上に効果的に寄与します。
- レポートを通じて、生産ラインの実情や稼働状況を正確に把握することが可能です。この情報を活用することで、生産工程の効率化やパフォーマンスの最適化を実現し、全体的な業務の精度とスピードを向上させることができます。
特徴・導入効果
1. 少ないデータで手間をかけずに高精度なモデル構築
DeepInspectは、最小限のサンプルデータからAIモデルを効率的に学習させるために、独自のディープラーニングアルゴリズムを採用しています。必要な学習データが200枚未満で済むため、データ収集にかかる時間とコストを大幅に削減可能です。また、良品学習方式を採用しており、個別のタグ付けや複雑な前処理が不要です。その結果、データ準備に伴う労力を最小限に抑え、短期間でのモデル構築が可能となります。
2. 迅速な導入プロセス
DeepInspectは、複雑なカスタマイズを必要としないため、短期間で現場に適応できるシステムを構築可能です。さらに、PLCとの連携機能を標準装備しているため、既存の生産ラインにスムーズに組み込むことができます。この結果、システム導入後すぐに生産効率の向上を実感でき、現場のオペレーションに貢献します。
3. 直感的な操作性
ノーコードで操作可能な使いやすいユーザーインターフェースを搭載しているため、AI技術者などの専門知識を必要としません。一般的なパソコンスキルがあれば、誰でも簡単に操作を開始できます。この簡単な操作性により、導入後の学習コストや操作ミスのリスクも最小限に抑えられます。これにより、現場スタッフが負担を感じることなくシステムを活用できる環境を提供します。
4. 外観検査以外の検査にも対応
DeepInspectは、外観検査に加えてOCR(光学文字認識)やOCV(光学文字検証)といった文字認識機能を備えています。また、画像内に含まれる特定のオブジェクトの数を正確にカウントする機能も搭載しており、多様な検査ニーズに対応可能です。これにより、従来の目視検査では難しいタスクを自動化し、生産性と品質管理をさらに向上させることができます。
このように、DeepInspectは少ない労力で高精度な結果を得られるだけでなく、現場の即戦力となる柔軟性と使いやすさを兼ね備えたソリューションを提供します。
自動車
CASE1:油圧フィルター検査
直面していた課題
オイルフィルターの欠陥(凹み、切れ目、不適切なシール、ネジ山の欠如、損傷したケーシングなど)は、異物除去不足やオイル漏れを引き起こし、エンジン性能の低下や可動部品の摩耗を早める原因となっていました。さらに、不十分な潤滑や摩擦熱の増加によりエンジンがオーバーヒートし、部品の歪みや故障を招く可能性が高まり、車両全体の信頼性と寿命に大きな悪影響を与えていました。
解決のための工夫と結果
DeepInspectを中心としたAI外観検査システムでは、4台のサイドカメラと1台のトップカメラを活用した360度の包括的な検査と、効果的な照明配置による可視性向上を組み合わせ、事前学習モデルを用いて最小150ミクロンの欠陥まで正確に検出しました。これにより、99.5%を超える検出精度と0.5%未満の誤検出率を達成し、製品の品質を向上させるだけでなく、人的エラーを排除して生産効率を高め、欠陥のない製品のみが顧客に届けられる信頼性の高い生産体制を実現しました。また、法令遵守やブランド評価の向上にも貢献しました。
CASE2:ガスケットの複数欠陥検査
直面していた課題
ガスケットメーカーは、従来の画像検知システムが異なる検査項目ごとに個別のカメラとセットアップを必要とし、その結果、システムの構築が複雑化し、セットアップ時間や導入コストが増加していました。この非効率性により、表面欠陥や部品の位置ずれ、印字内容の誤検出が発生し、製品性能の低下やシール性の不具合、サプライチェーンの混乱といった重大な品質問題が生じ、顧客の信頼やブランド評価が損なわれるリスクがありました。
解決のための工夫と結果
DeepInspectシステムは、効果的な照明配置と高度なAI技術を組み合わせることで、1台のカメラで複数の検査項目(物体の数え上げ、表面欠陥の検出、印字内容の認識など)を同時に実行可能にし、99.5%の高精度を達成しました。このシステムにより、セットアップ時間を大幅に短縮し、検査コストを削減、ヒューマンエラーを排除しつつ、生産ワークフローを効率化しました。さらに、150ミクロンの欠陥を識別可能な精度により、製品の一貫した品質を保証し、ブランド価値と顧客満足度の向上に貢献しました。
一般消費財
CASE1:空ガラス瓶の検査
直面していた課題
ガラス瓶の表面欠陥や内部の異物(ガラス片や昆虫など)は、消費者の安全を脅かし、製品の品質やブランドの信頼性を損なう重大なリスクとなっていました。また、透明性や形状の複雑さ、底部検査の限界などにより従来の画像検知システムでは欠陥検出に課題があり、不十分な検査が規制違反や市場での評判の低下を引き起こす可能性がありました。特に化学物質の溶出や異物混入による健康被害が懸念され、効率的で信頼性の高い検査システムの導入が急務でした。
解決のための工夫と結果
DeepInspectシステムを組み込み、4台のカメラを用いた全方位検査と効果的に配置された照明によって、透明性や形状の課題を克服し、99.5%の精度と0.1%の誤検知率で欠陥や異物を正確に識別しました。これにより、致命的な不良品を排除しつつ、1分間に400~450本を処理する高速な検査ラインを実現しました。また、人的作業を削減し、運用コストを最小限に抑えながら、規制遵守と顧客の安全確保、高品質な製品の安定供給を可能にし、ブランド評価と運用効率の向上に大きく貢献しました。
CASE2:ビスケットの検査
直面していた課題
ビスケット製造業者は、製造過程での割れや加熱不足、異物混入、ロゴの不一致、表面欠損などの問題により、顧客からの苦情や規制違反のリスクにさらされていました。これらの未検出の欠陥は、製品の返品や顧客満足度の低下につながり、ブランドの信頼性を損ない、結果として事業収益に深刻な悪影響を及ぼしていました。また、衛生基準を満たさない製品が市場に出回ることで、消費者の安全や健康にもリスクが生じていました。
解決のための工夫と結果
DeepInspectを用いた、AIを活用した革新的なビスケット検査システムにより、180~200個/分の高速ラインで多様な欠陥や異物を正確に検出し、欠陥品を自動的に排除する仕組みを提供しました。このシステムは45分以内でモデルをトレーニング可能で、標準的な画像200枚以下で高精度な検査を実現し、人員削減と労働コストの最適化を達成しました。さらに、0.5%以下の廃棄率を維持しながら、生産効率を向上させ、安定して高品質な製品を提供することで、顧客満足度とブランドの信頼性を大幅に向上させました。
製薬
CASE1:ゼラチンカプセル検査
直面していた課題
カプセルの変形、表面欠陥、気泡、漏れ、変色などの欠陥があると、製品の保存期間が短くなったり、投薬量の不一致、有効成分の劣化などの影響がありました。これらの検査は従来、熟練した作業員が目視で行っており、非常に多くの時間と労力を要するだけでなく、人手に頼った作業による欠陥の見逃しやミスのリスクも課題となっていました。
解決のための工夫と結果
DeepInspectシステムを組み込み、照明とカメラを垂直に配置し、その間に透明なコンベア上で検査物を流すという自動検査システムを導入しました。この仕組みにより、表面の欠陥を明確に検出することが可能になり、人手による検査の負担を大幅に軽減しました。結果として、1分間に1,000個以上のカプセルを処理することが可能となり、気泡、二重カプセル、サテライト、黒点、変形などの欠陥を99.95%の精度で検出することに成功しました。これにより、従来の人手に頼った検査では実現できなかった効率と正確さを達成しました。
CASE2:シロップキャップ検査
直面していた課題
シロップキャップには、へこみ、切れ目、シールの欠如、不適切なシール、ネジ山の欠落などの欠陥が発生し、これが内容物の汚染や漏れのリスクを高め、細菌や空気にさらされることで製品の品質が損なわれ、消費者の健康に悪影響を及ぼす可能性がありました。また、これらの欠陥が製薬規制に不適合となることで罰金やリコール、ブランドの評価損失といったリスクが生じ、最終的には消費者の信頼低下や売上への悪影響が避けられない状況でした。さらに、従来の人手による検査は非効率で、ミスやコスト増加が業務の課題として残されていました。
解決のための工夫と結果
これらの課題に対して、DeepInspectシステムを導入し、2台のサイドカメラと1台のトップカメラを使用した360度検査を行うことで、キャップのあらゆる角度から欠陥を正確に検出可能にしました。効果的に配置された照明により、詳細な画像を取得しやすくし、自動化された検査プロセスによって手作業を削減し、人為的エラーを最小化しました。その結果、欠陥検出率は99.5%以上に向上し、微小な欠陥も正確に識別できるようになり、誤検出率も0.5%未満に抑えることで不要な廃棄を大幅に削減しました。このシステム導入により生産効率が最適化され、完璧な製品のみを顧客に提供できる環境が整い、ブランドの信頼性と評判を強化するとともに、厳格な品質基準や規制要件を確実に満たすことが可能となりました。